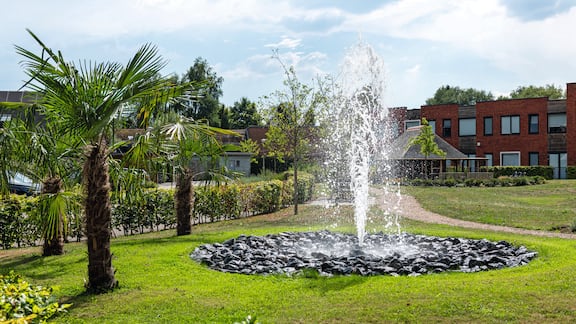
Where work is fun
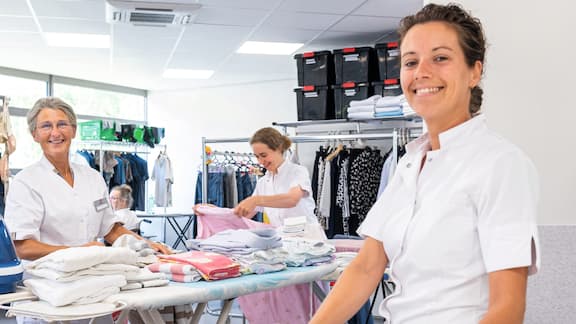
The atmosphere among employees in the laundry is good. It may sound trite, but it hits you immediately. The three employees Anja, Teuny and Sabine are busy ironing laundry. 'The laundry is designed to support our every move, says Teuny'. All three have arranged their ironing boards in a triangle. This allows the team to chat while they work. It is precisely this interaction which ensures a pleasant working climate in the laundry of the Elim retirement home in the Dutch town of Barneveld. Teuny confirms this: 'Since refurbishment and modernization, work is much more fun'. The atmosphere and layout of the premises are conducive to good communication. There is plenty of space and room to move around.
Anyone who has worked in a laundry knows full well that aspects such as providing sufficient space and good lighting can be challenges. Henry Vos, technical manager at the facility and, inter alia, responsible for the laundry, is also satisfied. He was commissioned with looking into whether the modernization of the 17 year old laundry would make economic sense or whether residents' laundry should be contracted out to an external service provider. The objective of his analysis: More efficient processes, improved workplaces and, of course, top quality in the reprocessing of laundry.
More in need of care, fewer carers
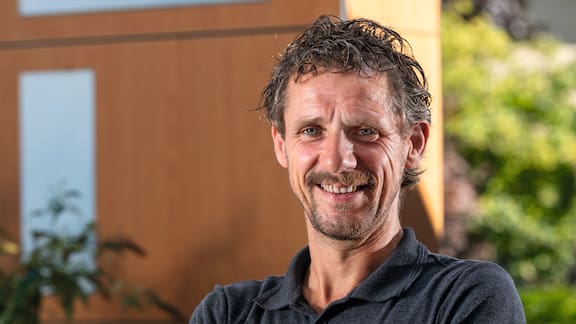
Henry Vos is the sort of technical manager who is familiar with every single cable shaft in the entire building. He is even greeted by the residents. And his co-workers say a cheery 'Hello'. The laundry is close to his heart. That is evident when he talks about modernization measures. He is employed by the Sirjon group which runs 20 retirement and care homes in the Netherlands. Elim in Barneveld is one of them. Demand for places in the home is large. This approach to holistic development and an analysis of the laundry set the ball rolling: 'On the one hand, there is a dramatic increase in the number of residents requiring care. On the other, it is becoming increasingly difficult to find and retain staff in the care sector. It is also my job to plan the deployment of staff as efficiently as possible.
The technical manager, like many others with a responsibility, feels the pressure in the branch. Some are quick to call for job cuts and outsourcing in care. But those calls fell on stony ground from the outset in Henry Vos' case. 'When reprocessing residents' laundry, the focus must always be on quality. I would have been loath to outsource the personal clothing, towels and bed linen of our residents'. Henry Vos contacted the Dutch company Intrakoop, a sort of consultancy for care and nursing homes which provides support in transformation processes – from energy issues to personnel – and has access to a large partner network of specialists. One of the partners in this network is Miele. The company agreed immediately to scan the laundry and highlight new avenues and opportunities. 'This collaboration was a stroke of luck', says Henry Vos, looking back. Miele recommended that we enlarge and modernize the premises.
Joint calculations revealed that an on-premise laundry would still be cheaper for Sirjon than ploughing work out to an outside laundry.
Employees have a say
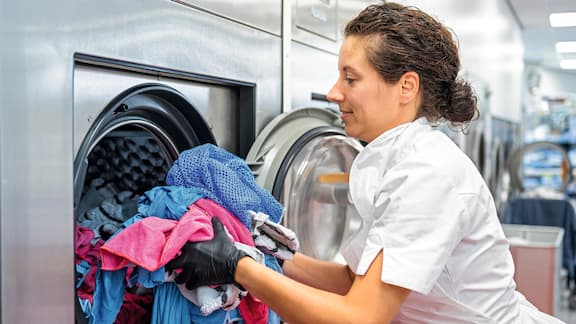
Thanks to clever structural changes, the previous 75 m2 of space was increased to 110 m2, allowing greater efficiency. And much thought was given to the employees. Vos stresses: 'I am responsible for working conditions and wanted to grasp the opportunity to make the best of the space available.'
The very fact that employees in the laundry can have lively conversations while washing machines and tumble dryers are running is the result of one of the central features of the modernized laundry which was the brainchild of Henry Vos: a so-called 'klankkast' – an encapsulation of Miele machines to reduce sound emissions. This signals a battle against noise which creates stress and represents an important move towards health protection. Making sure things are different in Elim. All machines and surfaces are ergonomic and designed to virtually eliminate bending and lifting. The tables in the laundry, too, are all height-adjustable, allowing folded laundry to be transferred from the ironing board to the tables in a smooth, sweeping movement.
The laundry as part of a whole
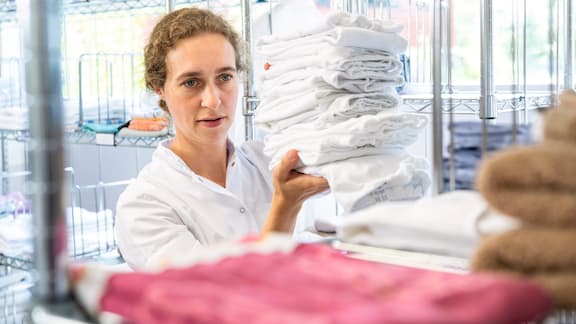
Henry Vos and the planning team had another brainwave: Alongside large windows, LED daylight lamps ensure uniform lighting and create a pleasant atmosphere. Vos appears full of pride when he claims: 'We have got the most out of the refurbishment and can now offer a laundry service with top-class quality and logistics'. Within a turnaround time of two working days, we supply residents and employees with clean laundry'. But there is something else which makes the Elim care home such an exceptional location for a laundry: Elderly residents have the opportunity to help out by folding laundry at an additional workplace. This, too, results in a feeling of belonging and recognition.
This article is part of our customer magazine "PROconcept". Feel free to download the digital version of the magazine.